Test & Sim
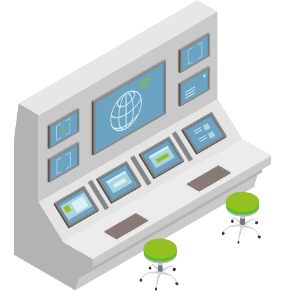
ARINC 818 test and simulation tools are indispensable for developing and validating high-performance digital video systems in aerospace and defense. These tools enable engineers to thoroughly test, verify, and simulate ARINC 818-based systems across various stages of development, ensuring reliability and compliance with stringent industry standards. Whether in simulation labs, production environments, or automated test equipment (ATE) setups, ARINC 818 testing supports mission-critical applications that demand precision and robustness.
- Techway Switch
- ATEs
- Production test
- Verification & validation
- Simulation Lab
Key tools in ARINC 818 test and simulation include frame grabbers, graphics generators, protocol analyzers, and scripting languages. Frame grabbers capture and analyze ARINC 818 video streams for detailed inspection and debugging, while graphics generators create video patterns to test display systems. Protocol analyzers validate adherence to ARINC 818 specifications, and scripting languages automate complex test sequences. These tools streamline workflows, reducing development cycles and enhancing the performance of ARINC 818 systems.
Test and simulation environments are critical in verifying and validating systems such as cockpit displays, mission recorders, and sensor payloads. Simulated testing replicates real-world scenarios, allowing engineers to detect and resolve issues early in the development process. The ability to test with precision ensures these systems meet operational requirements, delivering the reliability and robustness necessary for aerospace and defense applications.
Discover the complete set of test and simulation tools available:
Protocol Analyzers
An ARINC 818 Protocol Analyzer captures ARINC 818 video and provides a complete analysis at the byte, ADVB frame, video line, and video frame levels to verify ADVB packets to assure that they align with the ARINC 818 standard and protocol. Additionally, it evaluates line and frame timing, unlike FC analyzers, which are data centric.
Frame Grabbers
Frame Grabber cards are used to transmit and receive ARINC 818 video streams. They convert video, are video generators. Frame Grabbers are used in multiple phases of an aerospace engineering program to include; engineering, simulation labs, qualification testing, flight testing and production testing. They are used in large area display (LAD) and conventional display development, avionics video, ATP for production displays, and cockpit simulators. These cards test ARINC 818 systems and diagnosing the health of the video links.
Common features:
- Frame Grabber, Video Generator, ARINC 818 to/from DVI
- Full-featured test applications
- Optional Windows and Linux SDKs available
Switches
Switches can provide real-time ARINC 818 switching, splitting, or broadcasting. Most ARINC 818 switches are built with FPGA technology and provide high-density optical interfaces. Switches maintain real-time switching without interruption to ensure that video frames remain intact and are not corrupted. ARINC 818 switches are used in many avionics applications.
Converters
ARINC 818 converters can be either stand-alone modules or embedded products. They offer flexibility in converting to or from ARINC 818 in a variety of video formats such as DVI, RS-170, STANEG 3350, HD-SDI, and VGA for flight in both commercial and military applications. Converters may be used to generate test patterns for continuity tests and equipment checks.
Robustness Tools
Robustness tools can quickly test nearly any ARINC 818 interface. With these tools, you can test ARINC 818 receivers in cockpit displays, flight recorders, or switches. A user can easily inject multiple types of errors into an ARINC 818 stream. Packet CRC errors to all ADVB frames or to selected frames; Ordered Set Errors (missing or corrupted ordered sets), container count errors, and sequence count errors. Create configurations with slightly different frame, line, or image timing. Robustness tools are invaluable in validating the robustness of an implementation against errors and timing variation. It is also used during DO-254 validation to generate error sequences that trigger fault logic.